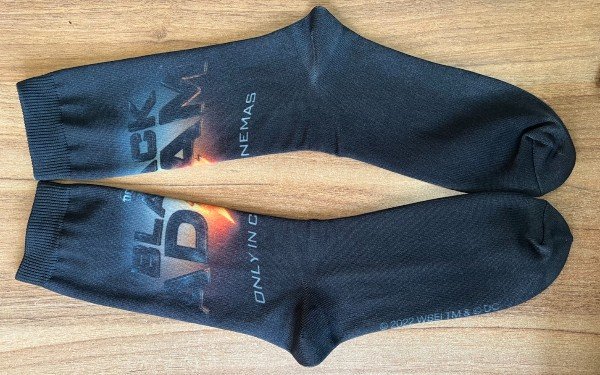
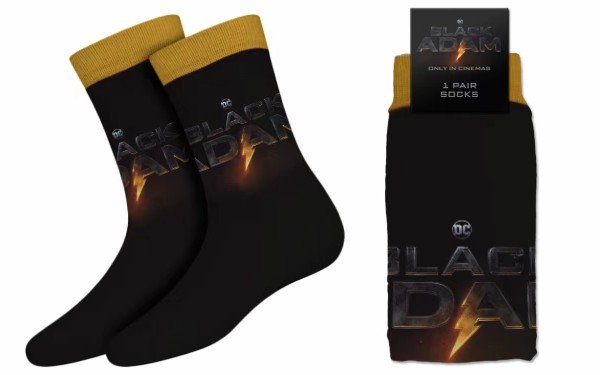
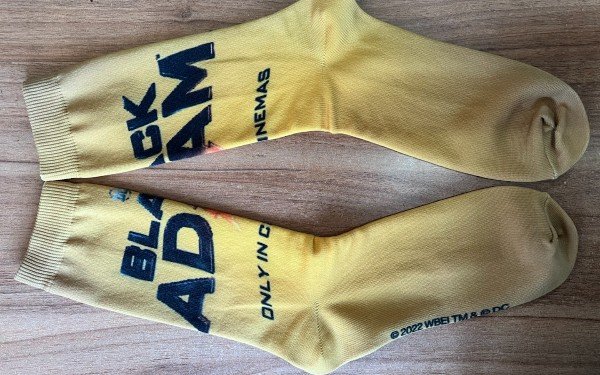
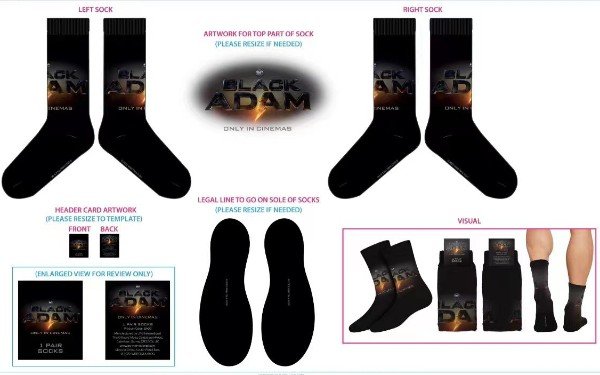
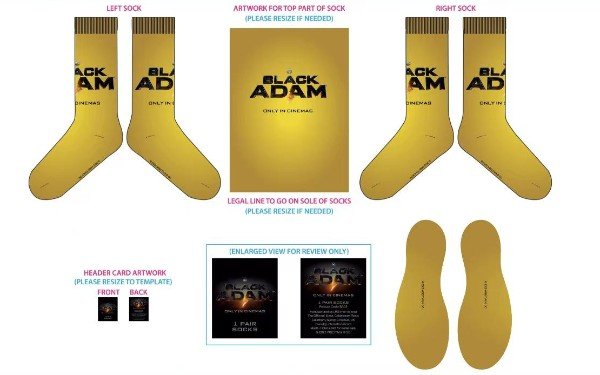
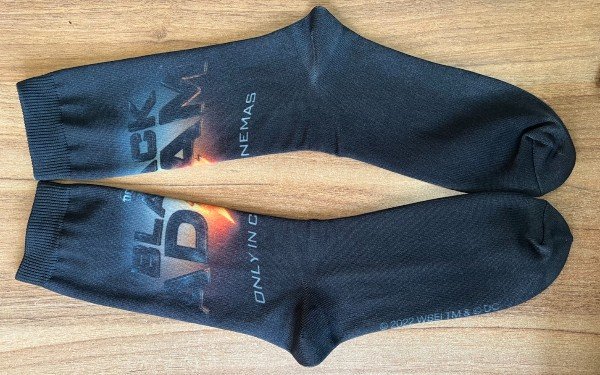
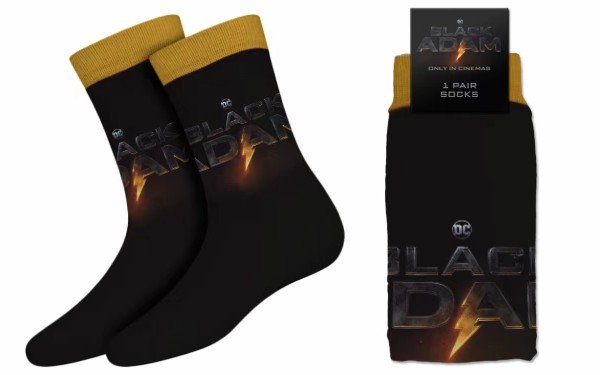
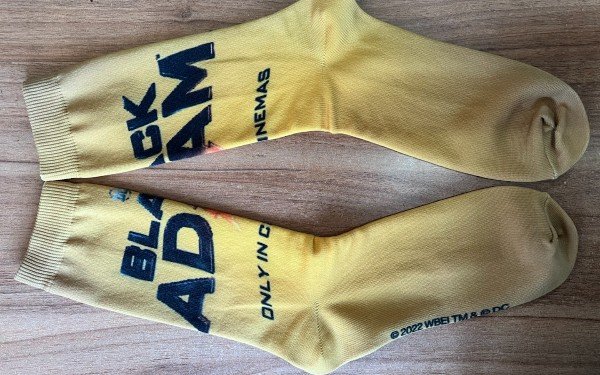
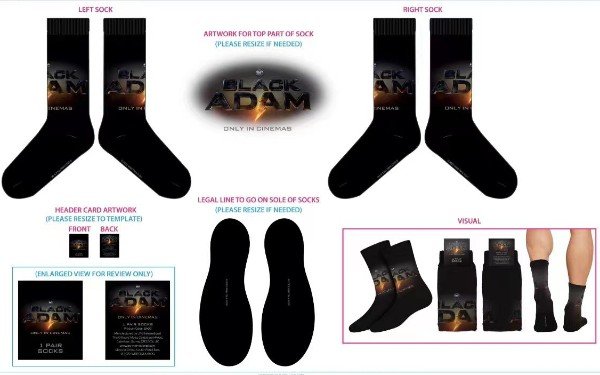
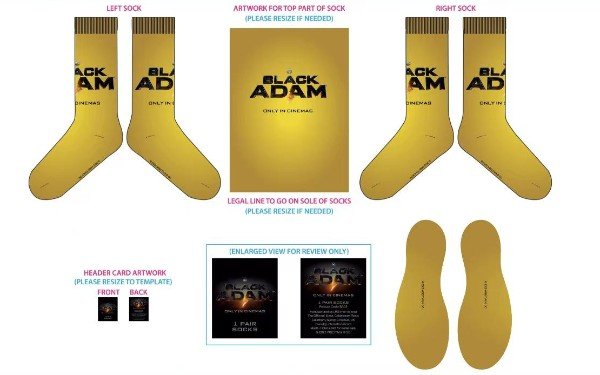
Customize Black Adam Socks
2. The printing process can be somewhat flawed and the standard of each production run is not well controlled.
Process
Client Background: LRG International is a multi-award-winning, environmentally friendly, global marketing and sales promotions business. It partners with a diverse range of companies across a spectrum of industries, supporting both their domestic and global marketing strategies through a wide variety of engaging merchandise, bespoke POS, and creative brand solutions. It works with Hallosourcing mainly to do customization of film peripherals.
There are many cases of cooperation between ruizhi sourcing and LRG International, such as the following successful brand customization cases:
1. 2022-04-09 The client gave the initial product requirements. We gave the client an initial quotation on 2022-04-12.
2. 2022-05-13 The client provided the design and started preparing the proofs.
Below is the design draft of Black Adam socks:
1. After confirming the client’s design, the original supplier confirmed that the product could not be completed and we started to find a new supplier to quote.
2. We updated the quote for the client.
19th,May, Arrange proofing
27th,May, Samples were made and sent to the client.
Black adam-width:18.8cm; height:6.5cm
only in cinema-width:12.2cm; height:0.5cm
legal line-height :0.3cm*width:12.6cm
![]() |
![]() |
Black | Yellow |
The client placed an order for **** pairs of socks.
Hallosourcing received pre-production samples.
![]() |
![]() |
Pre-production samples | Sample |
Problems:
The pre-production sample received was greener in color compared with the previous sample. After communicating with the supplier, it was confirmed that the problem was caused by an ink problem. As the original ink supplier had stopped production, the sock supplier had to find a new supplier to produce. The ink in this batch was not the same as the previous one. It was the same for fabrics, there would be some color variation between batches, but the same color can be guaranteed for the same batch.
Client’s feedback:
1. The client was very dissatisfied with the effects of the pre-production sample and refused to accept it.
2. The overall effect of the pre-production sample printing is not as clear as the sample socks.
3. The color of the letters is so close to the background color that the letters are barely visible; the effect of the glowing part is also not obvious; grey needs to be shown behind the letters.
The supplier redid the pre-production sample (as shown in the picture below).
1. Confirmed samples
2. First pre-production sample (denied)
3. The newest pre-production sample
1. 2022-07-14 The client confirmed that the samples needed to be sent, and after they received the samples, they would confirm whether the mass production could be arranged.
2. 2022-07-18 The client received the samples and confirmed that mass production could be arranged.
We confirm with the client how the socks would be packed.
1. fold the card in half + put a pair of socks in an OPP bag
2. put 25 pairs of socks into a large OPP bag
3. put the socks into the K+K standard export carton
4. 200pcs/CTN
![]() |
![]() |
![]() |
The client wanted to arrange for our QC to inspect the goods, but since the factory is in Zhejiang Province, it would be very costly to send our QC to inspect the goods. Therefore, we suggested the client use a third-party company with whom we have a cooperative relationship to inspect the goods. The cost of inspection ***USD needed to be confirmed by the client. The client disputed the cost of the inspection and eventually decided to arrange his own QC inspection and confirmed that the goods would be inspected by a third-party inspection company V-Trust on 2022-08-02.
1. The third-party QC confirmed that the goods passed the inspection and waited for the client to confirm the final inspection result.
2. 6 pairs of socks had minor defects on inspection and the client wanted to know how we dealt with these minor defects. The supplier verified that the minor defects were printing problems and could not be fixed. The supplier made an extra 20 pairs when making the mass production and these 20 pairs would be given to the client as spares free of charge. The client accepted our solution.
Aug 4th,2022 Shipment of goods.
Summary:
1. This order went relatively smoothly overall, based on the fact that Hallosourcing had stocked a few good suppliers from its previous work on custom socks. They were able to respond quickly to the client’s request to arrange samples.
2. The whole delivery process was flawed: the factory was not strict enough in controlling the quality of the products, resulting in serious discrepancies between the first pre-production sample and the initial sample. We have been working on the principle of treating our clients sincerely, informing them of problems and solutions, and strictly controlling the quality of our products so that the second pre-production sample meets the acceptance criteria.
However, this process resulted in wasted time and express shipping costs and did not satisfy the client in one go. We need to sum up our experience and lessons learned and continue to be strict in the process of subsequent orders to achieve high efficiency, and high quality and reduce unnecessary expenses.