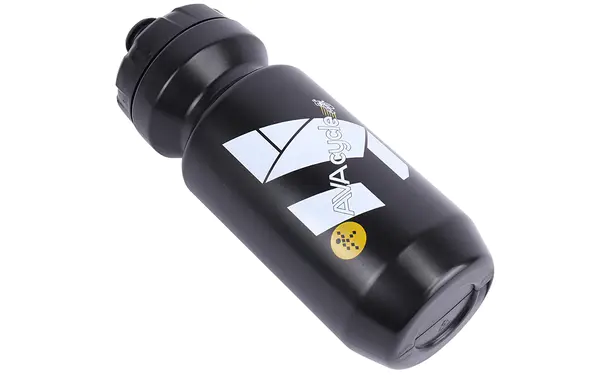
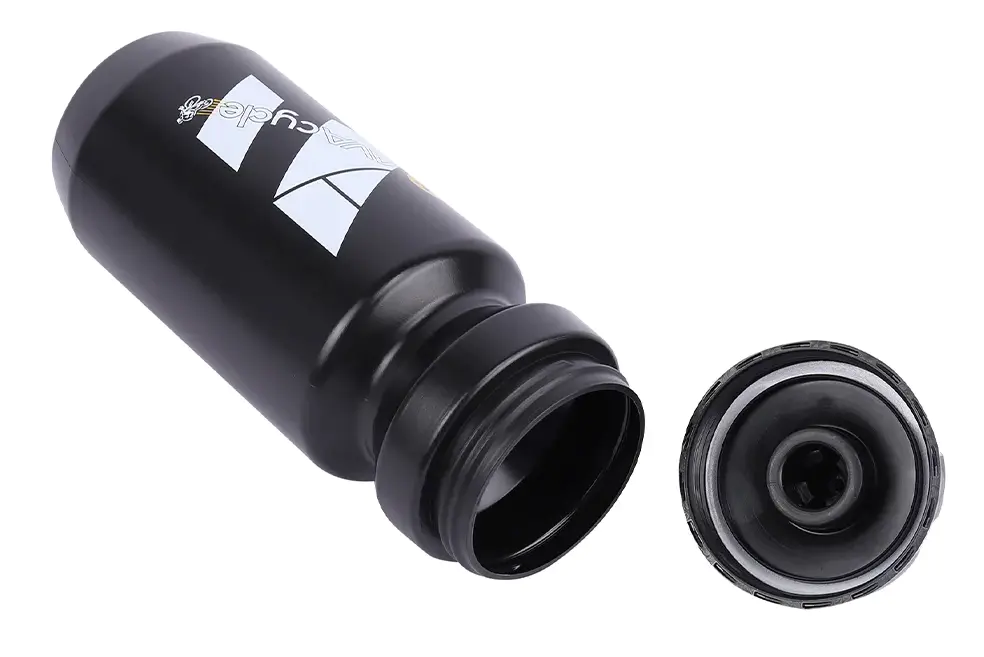
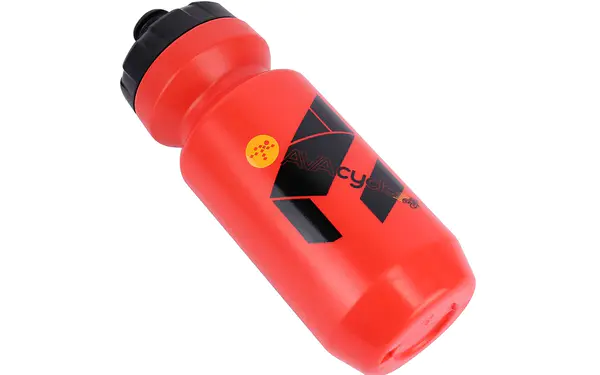
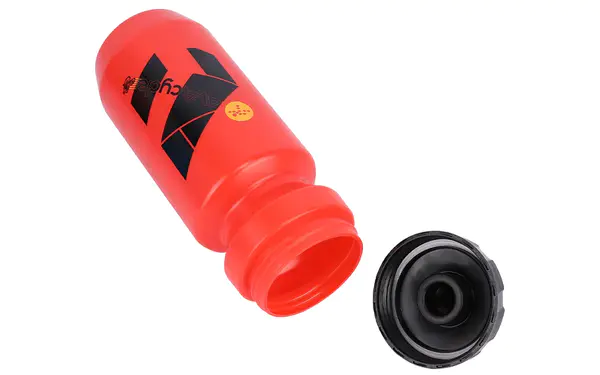
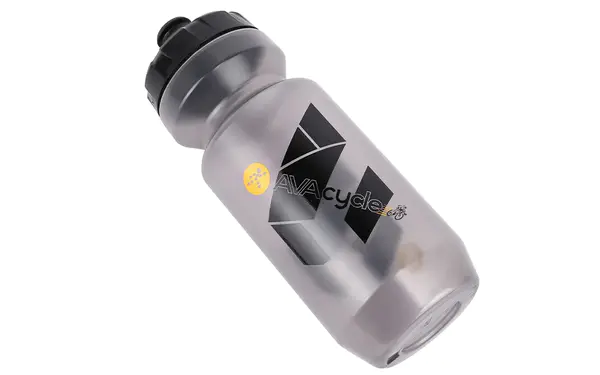

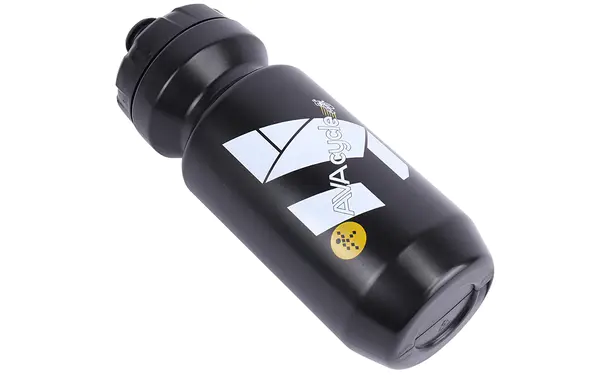
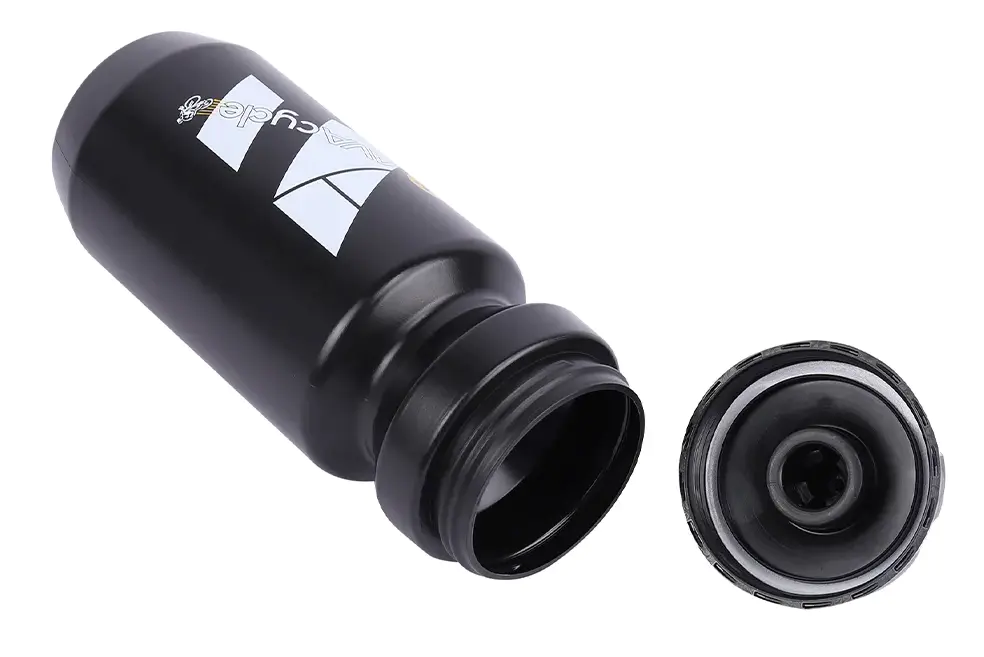
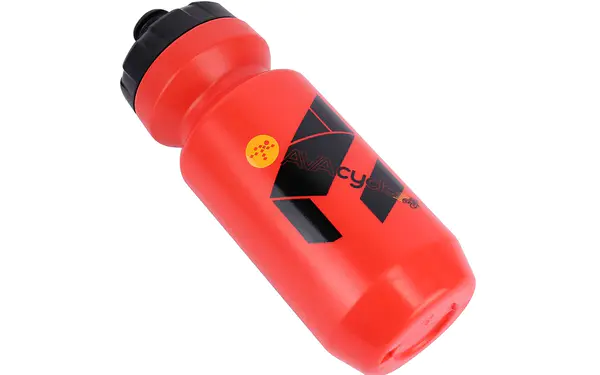
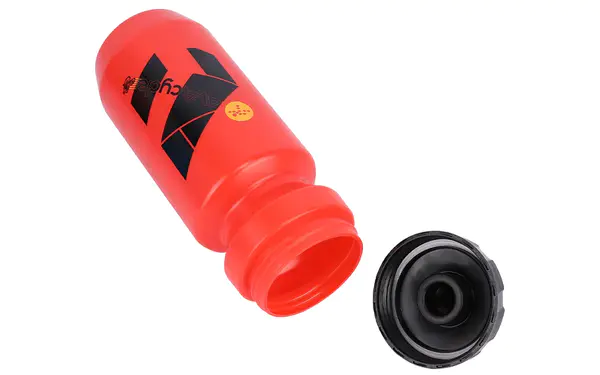
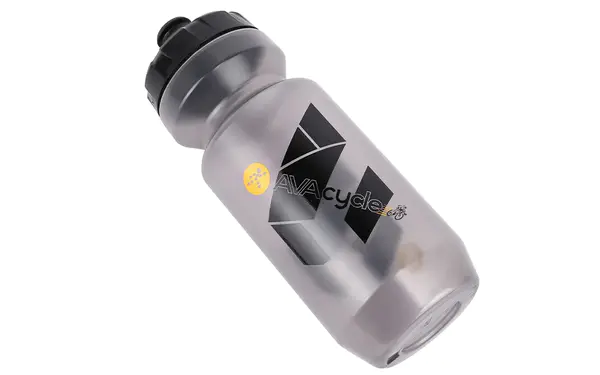

Bicycle Water Bottle Return Order from Vietnam Dienmayxanh
- Original supplier price increases
- customization does not meet the minimum order quantity required by the factory
- replace the packaging with the Client’s requirement
- urgent delivery after order confirmation
Process
Background: Dienmayxanh(DMX) part of the MWG Group, is the largest local home appliance retailer in Vietnam, with more than 1,000 shops opening in the country by 2020. It not only has a nationwide chain of shops, but is also popular for online shopping. Dienmayxanh also deals in bicycles and bicycle accessories. DMX ordered a shipment of bicycle water bottles in July 2021. When the bottles arrived in Vietnam, they were well received by the consumers and passed the local certification, and DMX decided to return the order for these bicycle bottles with their own logo, Hallosourcing is required to deliver 10000 units in accordance with the required delivery time and customization requirements.
Jan 10th, 2022 The product was first delivered with 4,000 pieces to the client’s appointed forwarder.
Mar 25th, 2022 The remaining 6,000 pieces were sailed out of the port.
Online and offline listing and sales by DMX
![]() |
![]() |
![]() |
Black | Red | Transparent |
When communicating with client Dienmayxanh in Vietnam, our client put forward the following requirements:
![]() |
Exported Countries: Vietnam
Product: Bicycle water bottle Quantity: 10000pcs Requirements:
|
Chat Record with the client | Order requirement |
We had initial conversations with each of the three factories that we work with in the company’s old and new supplier pool (Introduced a new supplier to quote, increase price bargaining chips and reduce delivery risk) about the details of the products to be confirmed and the customization requirements and possible difficulties that may exist.
Water bottle brand manufacturer–Dongguan **** Bicycle Co.
Water bottle manufacturer–Shenzhen **** Plastic Products Co.
Water bottle packaging factory–Shenzhen **** Packaging Material Co.
I. The client asked for the product to remain at the original price. The previous supplier requested a price increase
Problem: Upon receipt of the client’s order request, Hallosourcing immediately contacted the supplier we had previously worked with to discuss the details. However, the business negotiation was not a happy one, as the original brand partner requested a price increase due to rising raw material prices. As the first batch of bicycle water bottles were already well received by consumers, both in terms of quality and price, the client wanted to expand sales on top of this and had to keep the original price.
Solution: After repeated communications with the client, in order to better promote and sell the product and achieve a win-win situation, the unit price could only be remained at the original price. In view of the fact that the return order did not require a water bottle with the brand’s logo, Ruizhi Sourcing combined various resources and channels to finally find the bicycle water bottle production factory, eliminating the intermediate links of the brand, and got a price that met the client’s expectations.
Ⅱ. Bottle colour customization did not meet factory MOQ
Problem: As the order had four colours for each bicycle water bottle and required the same colour for the bottle body and cap, the factory required a minimum order of 3,000 pieces of a single colour. According to the order quantity, each colour of each model could not meet the MOQ production requirements.
Solution: The factory was introduced to the basic situation of the client in detail, so that the factory understood the strength and sales capacity of the client in Vietnam. We also explained that the order of 10,000 pieces was only for the client’s existing shops and that according to the client’s planning for 2022, the order was expected to be returned soon. The factory was persuaded to prepare the materials first and produce the finished products according to the order.
![]() |
How to negotiate with the factory to reduce MOQ, please click here |
III. Water bottle replacement packaging
Problem: The packaging for the first order of water bottles was relatively simple, using a generic size regular opp bag. The bag was on the large side with no closure, and the water bottle could easily fall out of the bag in transit. In this regard, the client offered to replace the closure bag and to customize the bag with their own logo.
Solution: In order to better serve our client, Hallosourcing agreed to the sudden increase in demand and immediately found a long-standing packaging factory to design packaging files in 30*20cm and 24*15.5cm sizes for the client to choose from, based on the existing product and the client’s requirements respectively. We also optimized the closure bags and made aeroplane holes in the bags so that the client could hang the product on the shelves and sell it. After confirmation from the client, we arranged for the factory to make a sample and take a video of the actual product to the client for reconfirmation before arranging for the production of large quantities.
![]() |
![]() |
![]() |
Neutral packaging | Design draft | Customized packaging for DMX |
IV. Urgent delivery after order confirmation
Problem: The order information was changed due to a change in the client’s counterpart and the client’s logo had to be changed for unexpected and irresistible reasons. The formal order was delayed in being confirmed. The formal order was signed at the end of the year and the normal production delivery time is 15-20 days. In view of the shipping schedule and the Chinese New Year in Vietnam, the client’s request to receive the goods before the Chinese New Year holiday was difficult to achieve.
Solution: Upon receipt of the client’s formal order, we immediately contacted the factory and asked for their full cooperation in giving the fastest possible production delivery time. At the same time, we consulted the freight forwarder about the latest shipping date. As the Chinese New Year was approaching, the shipping companies were bursting at the seams and the possibility of delayed sailing was very high. In order to ensure that the goods arrive before the holiday in the Vietnamese warehouse, they can only be loaded on 10 January at the latest. After consultation and communication with the client, it was decided that 4,000 pieces would be delivered first within 9 days. With the cooperation of the factory, the 4,000 pieces arrived at the client’s warehouse before the Chinese New Year.
![]() |
How to avoid the impact of Chinese holidays on import from China, please click here |