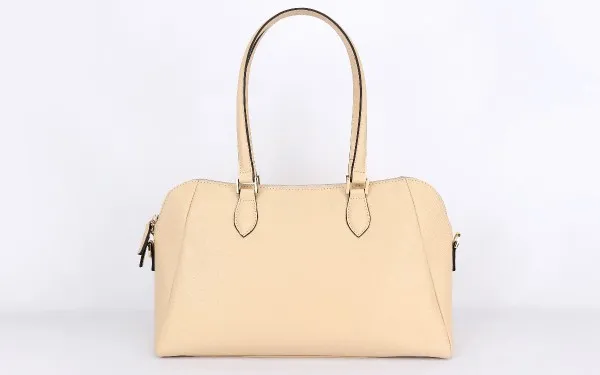
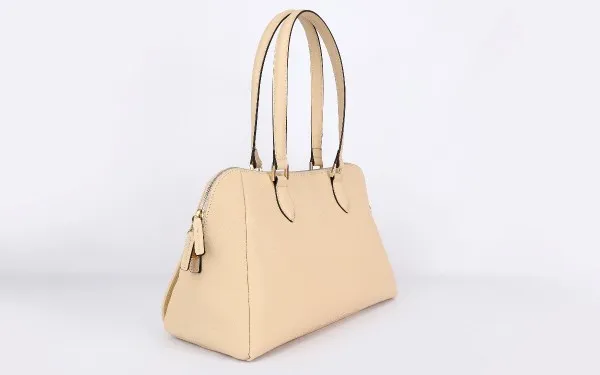
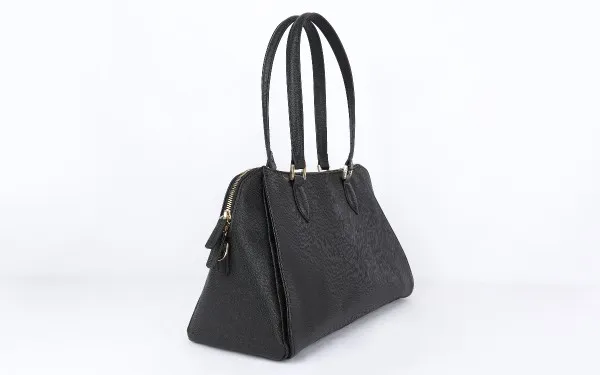
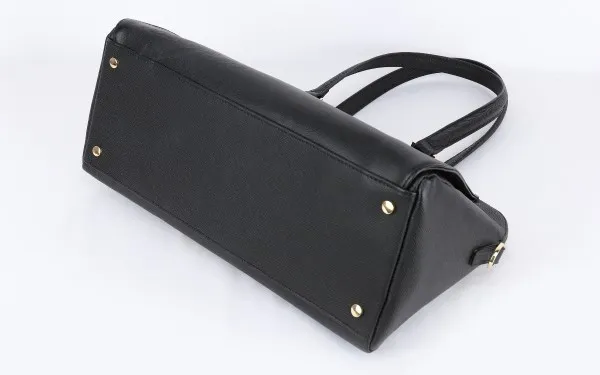
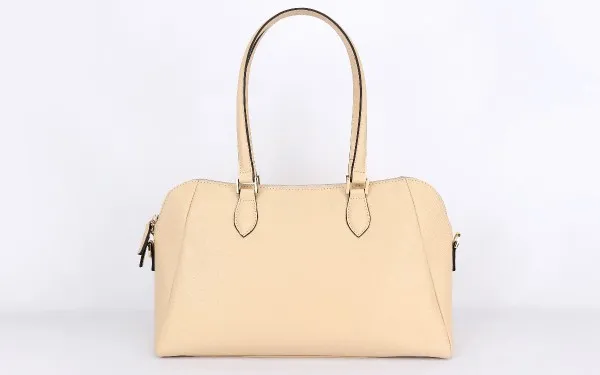
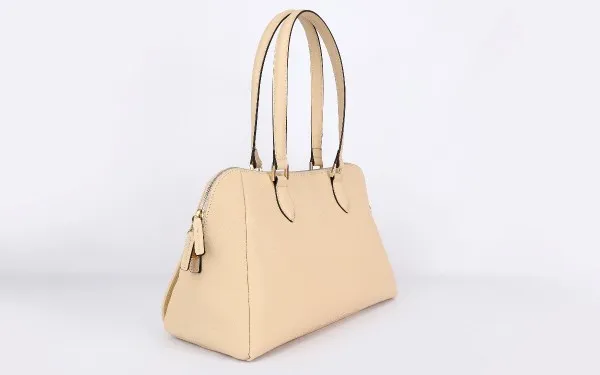
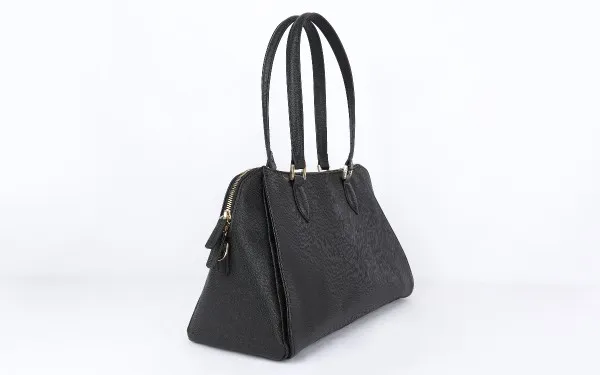
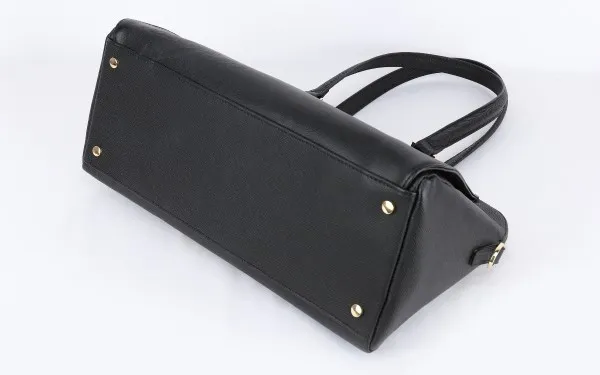
Customize Real Leather “Tuesday Bag” for US Client
2. The order quantity is too small, and it is difficult for us to purchase raw materials.
Process
Client background: high-end ladies’ bags in the United States retail through stores, e-commerce website and social media. Previously, finished products and raw materials were produced in Mexico and Europe, but due to quality control and production cycle problems, client began to produce in China.
Tips: Refer to the previous customized case for client’ monday bag.
17th.Jun, 2022
Our client e-mailed the product requirements for the first time, informing us that two samples of Tuesday Bag and Wednesday bag were arranged, and we were required to make corresponding changes according to the samples:
Product name: Bath sponge- bath sponge
Color: Black / Beige
Quantity: ***
Product requirements:
1. For fabrics: continue to use Monday Bag same fabric
2. Lining: continue to use the same fabric of Monday Bag
3. Need to add a key rope
4. The oute most pocket of the bag needs to add magnets, three on one side, a total of six magnets
5. Need to use the same shoulder straps as the sample, size & hardware, etc., need to be the same as the sample
6. Need to arrange black leather & beige leather & nylon material, one sample each
7. We need to confirm the size of the zipper required, the client will provide the zipper from other suppliers
8. Client confirmed through WhatsApp that the handheld strap needs to be lengthened.
- Confirm the proofing fee and do PI to the client.
- Confirm the details of the zipper with the client so that the client can arrange a suitable zipper to facilitate our proofing:
1. Confirm the Logo details with the customer:
The location is shown below and the font needs to use “Hatton Light”.
2. Confirm the length of the zipper:
Confirm that the required outer zipper length is 53cm and the internal zipper length is 23.5cm. It is recommended that client give more zippers as spare, in case the zipper is not enough when proofing; at the same time, client are required to send the zipper as soon as possible, so as not to affect the progress of the sample.
3. The client’s original zipper supplier could not provide it on time and adopted our Plan B:
The sample was originally scheduled to be completed on July 15, but the zipper was not sent in time because the client forgot to place an order with her supplier, which affected the progress of the sample. we recommends that client use our plan B zipper supplier, that is the handbag manufacturer’s own zipper, and the sample time is updated to 17th, July. However, if the client needs to use the zipper provided by her, then we need at least 7 days to receive the goods, and the sample will be delayed until the end of July. After discussion with the client, she confirms that the zipper of Plan B can be used to continue to arrange this sample:
1. We shot the difference between our sample and client’s sample.
We reveices samples of Tuesday Bag nylon handbags from client, compares our samples with customer samples, and takes relevant photos & videos to customers:
![]() |
![]() |
Appearance comparison | Suture contrast |
![]() |
![]() |
Bottom comparison | Zipper comparison |
2. The problems encountered are shown in the following figure. Due to manual proofing, there will be some imperfections. Machine production will be used in large goods, and the problem will be solved:
![]() |
![]() |
Sample comparison:The position of the zipper is not straight enough and there are waves: | Sample comparison:The shoulder strap position is not tight enough, raised, and not smooth enough: |
3. There are some differences in the manufacturing process between nylon handbags and leather handbags, as shown in the picture below.
Genuine leather: the leather material has a certain elasticity, and the joint can be folded and sewn directly.
Nylon: the fabric is inelastic. If it is made in the same way as the leather fabric, the finished product will produce a certain bulge, which will affect the beauty of the product. Therefore, in the process of making the interface, we add a connecting piece to fix it separately.
![]() |
![]() |
We talk to the client about these problem points, and the client is satisfied with the effect of our treatment.
The supplier informed us that there was a wrinkle problem on the surface of the real leather bag, and we went to the handbag production site to find out.
Problem:
The problem of surface wrinkling at the junction of real leather bags can not be avoided, as shown in figure 1 and figure 2
Reason:
Refer to figure 3, the picture is a sample of the inner bag of the handbag, in the process of making the handbag, the inner bag needs to be completed first, and all related sewing processes will be completed in this process. After completing the inner bag, the worker needs to flip the handbag, that is, turn the inner bag to the front. The leather fabric of this bag is hard and thick, and the size of this handbag is small, and wrinkles can not be avoided in the process of turning the bag. Because the beige color is light, the wrinkle problem will be more obvious.
Suggested solutions:
1. Find a fabric that is relatively soft, but needs the same color and the same surface texture.
2. In the process of looking for fabric, the sample master-designer will also try to use splicing processing (montage treatment) to find other solutions, but the splicing treatment will certainly change the overall appearance of the product, which needs to be confirmed by the client; and there will be corresponding proofing costs for re-proofing. we advises client to take a look at the actual sample effect made at present, and if there is any need to update, let them know at one time that we will improve all of them in the second sample.
![]() |
![]() |
![]() |
According to our previous sourcing service practice, for the finished product samples, we will arrange high-definition photos & videos to keep the bottom and provide them to the client for marketing. The product pictures taken refer to the product thumbnails of this case.
Tips: you can refer to our value-added services. Product shooting is one of our sourcing services.
After receiving the sample, the customer gives feedback: all the three Tuesday bag samples are deformed under pressure, as shown in the figure, the beige package is the most damaged:
![]() |
![]() |
![]() |
![]() |
The customer said that this sample is used for taking photos, and relevant photos and videos will be uploaded to the website and social media for marketing use. We apologize for the damaged bags, and we suggest that we airlift the bags we have left at our expense, so that client can take pictures and do later marketing. For the damaged packages that the customer has received on hand, we recommend that the client try to deal with them as follows:
Method 1:
Step 1: fill the bag with paper, especially in the corner
Step 2: with a hair dryer, blow the surface of the bag with hot air of about 35 degrees Celsius to make the fabric softer (note: do not blow too close, otherwise the surface will be damaged)
Step 3: after blowing the soft surface, straighten the surface and let it stand for 1 to 2 hours.
Method 2:
Step 1: fill the bag with paper, especially in the corner
Step 2: put a towel or cotton cloth on the surface and iron it with an electric iron (note: the electric iron should not be too hot, otherwise the surface will be damaged)
Step 3: after the surface is softened, straighten the surface and let it stand for 1 to 2 hours.
Previously damaged samples have been confirmed that it is difficult for client to return to normal state, The customer confirmed on WhatsApp that a Tuesday Bag sample needs to be rescheduled, requiring the use of original black leather and a stronger magnet, the zipper can use our existing Plan B zipper, and the zipper needs to be smooth. After the sample is finished, it will be sent directly to the client.
At 9th,Sep,2022
After the completion of the sample, we updated the product quotation to the customer, and made a price analysis on the Monday bag of the product and the initial order. The style and dosage of leather are similar to Monday Bag, but the price difference mainly comes from two aspects: material & craft.
Process details include: internal structure, premium rate of leather, scratch-proof fabric, hardware, strong magnet, internal addition of a zipper bag. The labor cost of the whole process is higher than that of Monday Bag. We received a quotation from the factory for customizing this real leather bag, but we felt that the price of this product was higher than that of the previous Monday bag, and the reason why we did not give the customer an offer as soon as possible was:
1. We want to know the actual effect of the sample and evaluate the finished product on the basis of customer market positioning.
2. Do price feasibility analysis with other suppliers, after comparing with serveral manufacturers, we found that the cost difference is not big.
It is finally confirmed that the current production cost of this bag is consistent with the customer’s positioning for the quality and price of the product, and finally we made this final offer to the customer. In addition, the factory confirms that the sample fee will be refunded when the order reaches 2000pcs.
1. The secondary sample is ready, and the physical picture is as follows:
![]() |
![]() |
![]() |
![]() |
![]() |
![]() |
2. To prevent the package from being crushed again, we has made improvements to the packaging:
The client contacts us via WhatsApp, she has received a second sample, and the sample is intact, she also likes this bag very much and wants to know if there is a way to reduce the initial order of bags and color boxes and arrange ** sets of Tuesday bag, use new color boxes and dustproof bags of the same style as Monday Bag, and want to know the price difference between ** sets and ** sets.
Tips: 7 ways to get low MOQ
We update the quotation to the client, because the bag order quantity does not reach the MOQ ***pcs, the price of **~** has no difference. But through the price comparison of the color box, we can see that the price has a very obvious difference.
As we all know, each product has its own initial order quantity and the royalty of the product is used as a fixed expense. when the number of products is large, the fixed expenses can be shared equally into the products, and the unit price of the products will fall; but when the number of products is small, even if the fixed expenses are shared among the products, the unit price will be very high.
For example, for the same color box, the royalty is 100USD, when the customer’s order quantity is 100pcs, the unit price is 1USD/pcs, but when the customer order quantity is 10pcs, the unit price is 10USD/pcs.
1. The client confirms the quantity and places the order
The customer confirmed that the order should be made directly to make ** Tuesday bag as bulk goods. In view of the fact that the box specification of the product is 8pcs/CTN, we suggest the customer to order **pcs, Form an integral multiple of a single package, do not have scattered, reduce transportation costs,The customer also confirms our suggestion. And signed a sales contract.
2. Customer updates order quantity of color box
In order to save the cost of color boxes, customer want to know if we can arrange ***pcs color boxes, in addition to the **pcs needed for large goods, the remaining ***pcs customer want us to airlift to her factory in Mexico (while cooperating with us, customer have cooperated with a small factory in Mexico, where small orders or new product development customer will put large orders for production in China when the order volume increases). After evaluation, we confirm that this solution is feasible and update the PI to the customer.
Tips: before the order is completed, every detail of the order may change, as sourcing needs to be adjusted to meet customer needs at all times.
The customer gives the design requirements of the color box: including the screen printing color number and packaging method of the packaging.
On the same day, according to the customer’s request, we made the effect picture of the color box as follows, and the customer also confirmed the design draft on the same day.
![]() |
![]() |
1. We have received the hand-made sample of the Tuesday bag color box, because it is a manuscript, the sample is a small machine and handmade, there are some defects, as shown in the following picture. In the process of bulk goods, all operations will be done by large machines, these issues will not exist next time.
![]() |
![]() |
![]() |
![]() |
2. The customer confirms that the leaf shape connection of Tuesday bag’s ear needs to be the same as that of Monday Bag. The reference is as follows. The picture on the left is Tuesday Bag and the picture on the right is Monday bag.
![]() |
![]() |
1. In the closing stage of the order, we provided the customer with a picture of the product and confirmed that the order will be inspected on December 5. Due to the small number of orders, we suggest that the goods be pulled from the factory car to the supplier’s office in Shenzhen, and the internal QC of Hallosourcing will do a full inspection. If any problems are encountered during the inspection process, they can be handled on the spot in the supplier’s model room. Through this way of inspection, it also saves the inspection fee for client, and full inspection can also bring more protection for client.
Below are pictures of the our sourcing QC checking the parts one by one after all the raw materials arrive before the final product is produced.
![]() |
![]() |
![]() |
![]() |
2. After communicating with the customer, the customer confirms that the they needs 6 pieces sent to them to do marketing first by air, and the remaining **pcs will arrange sea shipment.
3. The supplier informs the **pcs that there is a 6pcs in the factory that has failed the internal quality inspection and will give the 6pcs to us for final confirmation after completion. On the same day, we carried out a full inspection of **pcs and completed the quality inspection and passed the shipping standard:
![]() |
![]() |
![]() |
![]() |
![]() |
![]() |
![]() |
![]() |
1. We makes the final payment PI to the customer, which requires the customer to arrange the final payment before shipment.
2. On the same day, the 6pcs that needs to be airlifted was packaged as follows to ensure that the package will not be damaged during transportation.
![]() |
![]() |
![]() |
![]() |
Summary:
1. This order is customized for the customer’s second new product in our company. On the basis of the first cooperation, the manufacturer understands our product standard. This order is relatively smooth as a whole, although there are some problems encountered. But also have timely communication with customer and the problem has been solved.
2. In this case, due to the lack of sample packaging, the rough treatment of packaging and logistics, the customer received the deformed sample when signing for receipt, resulting in a delay in the progress of the project and resulting in a bad customer experience. We are well aware of the importance of samples and the efforts made by our customers, ourselves and suppliers for each product, so we take every step of product development carefully and seriously.
Once there is something wrong with the sample, it will cause trouble to many parties and bring unnecessary losses. Therefore, in the future packaging process, we should not only consider the transportation cost, and consider the feasibility of sample packaging, but also need to find a safe and reliable forwarder for delivery.
3. In the packaging process, we will seal the box, all need to take photos / videos to keep the bottom, to ensure that the products received by customer are packed in the same way as our shipments, and problems can be traced back to the source.
4. The development of this new product lasted nearly half a year, and it is more difficult to develop new products, so it is more important to communicate with customer continuously. We will maintain a certain degree of stickiness with customers and achieve timely response. Timely discovery, timely communication and timely provision of solutions.
This typical case can fully reflect how Hallosourcing helps our clients do the whole process of product development. I hope you can have a better understanding of how sourcing company helps you do product development and the problems that may be encountered in the process.